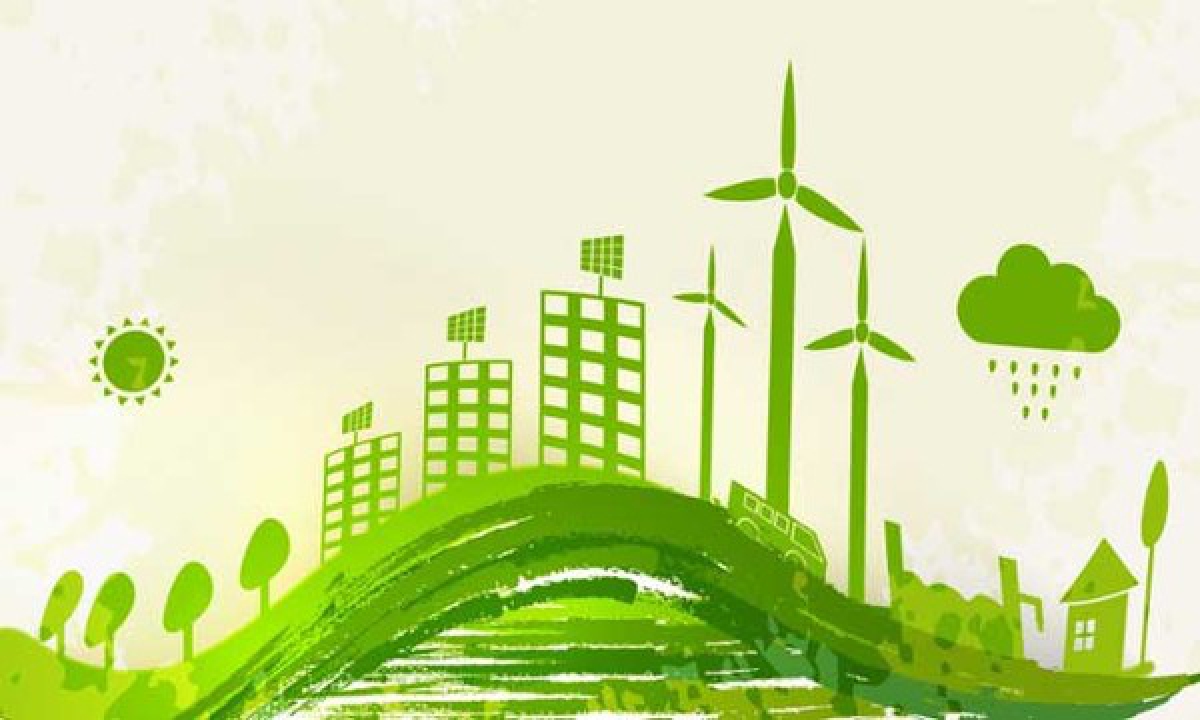
Impact of the Environment and Components on Durable Floors
Technology has allowed builders to measure and perfect the factors that help commercial buildings last longer. When it comes to facilities that require special environmental conditions, research can provide solid insights into how to build, which materials to use, and how to accommodate various factors to ensure a longer-lasting facility that will need fewer repairs over the course of the building’s use.
Basics like roof materials, wall insulation, and floors can make all the difference, particularly in facilities that have special temperature or weather requirements, or are located in particularly harsh climates.
Cold
Where there’s cold, there’s frost, vapor, and several other considerations that require a great deal of thinking before building. When it comes to the floor for a cold storage facility, indoor cold and outside heat causes moisture to want to flow from one place to another. To keep moisture under control, designers will use vapor barriers – sheets of plastic or other material that will keep vapor from migrating.
Planning and placement of vapor barriers is extremely important to the overall project from a number of viewpoints. Temperature and moisture control is important to the overall energy efficiency of the building, and controlling moisture properly will ensure a healthy environment with less opportunity for the growth of mold or mildew. While this is critical for safety in all facilities, it is particularly important wherever food is stored.
Facilities that are always cold can suffer from a never-ending frost cycle. As moisture seeps into concrete it builds up and then freezes; eventually it can cause large cracks or rifts in the floor. To mitigate this – depending on where your facility is and what the potential for problems might be – it is sometimes necessary to install heating elements or glycol warming systems under the floor.
Heat
There is a “concrete season” in some areas of the country. As Cement.org notes, when the thermometer climbs above 77 degrees Fahrenheit, and particularly if it gets above 90 degrees, concrete placement and finishing can be affected The site notes that experts should be on hand in high temperatures to make sure there’s a plan for everything from the concrete mix to the amount of water that’s being used; and from an approach to finishing that matches the finishing team with the demands of the temperature.
Moisture
The moisture content of concrete is very important. Each job requires just the right mix of materials and water that take into consideration all of the environmental conditions that can lead to a successful installation. As Concrete Construction points out, moisture has a great impact on the end result of a concrete floor – moisture can migrate to the surface and cause surface delaminations or cause a continual wet, slick area that is a safety hazard. These are all factors to consider in any kind of concrete construction project.
Outside moisture can hurt a floor, as well. As The Constructor notes in an article titled Factors Affecting Durability of Concrete, seawater exposure requires special attention to mix design of concrete to accommodate for the harsh chemicals in seawater along with the corrosive nature of water, which can freeze and thaw daily.
The Constructor article also notes that concrete is quite resistant to natural environments and chemicals, but it can be susceptible to sulfates and chlorides, so it’s important to consider what types of chemicals your floor may be exposed to and plan the right mix design to withstand potential corrosion.
Other factors that contribute to durability
The Concrete Thinker advises that concrete can crack and spall depending on a number of factors. Spalling can happen in cold climates where there is a great deal of freeze-and-thaw, or where there is too much water in the concrete mix.
As Cement.org notes, bugholes, small regular or irregular cavities, are another real problem. These small holes on the surface of the concrete can lead to flaking, cracks, and damage as traffic such as forklifts travel over them, greatly reducing the longevity and durability of the floor.
At FRICKS, we use our own lab to ensure the correct chemical components are in the mix for every concrete floor we pour. We’re focused on developing the highest quality concrete floors for clients that are right for the building, location, and the season the floor is installed. We have the technical skills and experience to make this happen every time.