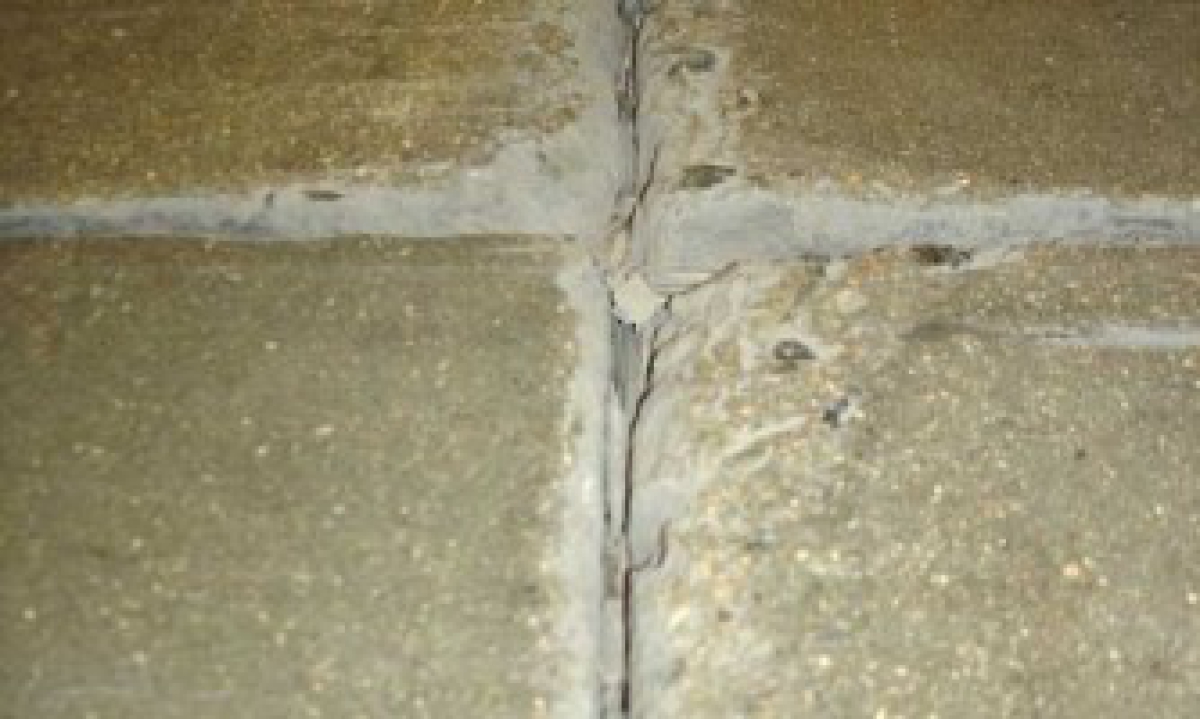
Techniques to Avoid Spalling in an Industrial Concrete Floor
Spalling is a serious concern for many facilities with industrial concrete floors that are designed or installed improperly. Spalling can cause forklift repair issues, accelerated equipment failure, increased dust and debris, slower daily inventory management, lower profitability and a variety of other problems. To avoid spalling, it’s important to understand what it is, what causes it and techniques that can prevent the need to repair or replace your floor.
What is Spalling in Joints?
Spalling is when a joint breaks down. The joint is a combination of the wall (face of the joint) and the slab on top. Whether it’s a control joint or a construction joint, it’s spalled once the corner of the joint is broken. Once that happens, it creates a weak point and exposed area for the slab. Over time, that area will grow wider and wider with continued forklift traffic, causing accelerated floor deterioration and expensive forklift damage as well.
What Causes It?
There are a number of reasons spalling can occur, but poor construction or poor design are at the top of the list. If the slab wasn’t designed, poured or finished properly, it can lead to a higher degree of curling. According to the National Ready Mix Concrete Association (NRMCA), “curling is the distortion of a slab into a curved shape by upward or downward bending of the edges. The occurrence is primarily due to differences in moisture and/or temperature between the top and bottom surfaces of a concrete slab.” Curling causes the joint to be more susceptible to spalling. Failure to maintain the joint filler is also a contributing factor.
How Do You Repair Concrete Spalling?
To repair concrete spalling, the affected area needs to be cut out as a square and then filled with rigid epoxy. This is only a temporary solution, however, since it has a limited life and needs to be maintained more often. It also needs to be inspected regularly and, if failed, replaced again. A better solution is to prevent spalling from happening in the first place by proper design, installation and maintenance.
Techniques to Avoid Spalling
Here are some techniques to avoid spalling:
- Proper design: The most effective technique for avoiding spalling is proper floor design. Specifically, designing a floor to accommodate a facility’s forklift and pallet rider traffic patterns. It also needs to compensate for moisture and temperature changes and the mix needs the appropriate amount of water, cement, aggregates and admixture.
- Proper finishing: Your contractor needs to utilize proper finishing techniques to mechanically densify the surface. The contractor also shouldn’t add water to the top; it may make it easier to finish, but it weakens the surface of the slab leaving it more prone to spalling.
- Maintain joint fill: Having a good monitoring and maintenance program for your joints is important. Make sure yours is thorough, documented, prioritized and consistent. For more on this topic, read the blog post.
- Working with the right contractor: A slab that’s curled is at a higher risk for spalling, so it’s important to work with an industrial concrete floor contractor that is good at reducing curl and gets the floor right the first time. The right industrial floor contractor will stabilize the slab so there is positive contact and the slab won’t rock (or lead to spalling).
Use armored joints at construction joints: Ideal for construction joints exposed to forklift traffic; armored joints are protected with steel to provide the highest level of durability and impact resistance for the most demanding forklift and pallet rider traffic patterns.
Spalling may be a top concrete floor concern, but you can avoid it with the proper techniques and partnering with the right floor contractor.